|

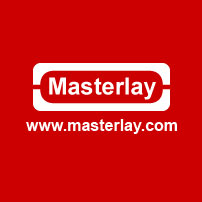 |
New company image
Welcome to the new Masterlay website. The desire for renewal and continuous improvement is an attribute of any good business.As an established lining contractor, we at Masterlay Limited wanted to take the next step in our development by associating our reputation for successful delivery with a strong individual corporate identity.
We selected a graphic design consultant that best interpreted our initial concepts and with them we have developed a brand that we feel is individual and distinctive. It is our intention to roll out the new brand across the business to ultimately incorporate a new logo, fleet livery, stationery, literature and this website.
The news page is an important feature of the website for us and it will be used to inform and update Masterlay Limited activities such as notable completed projects, significant developments and particular achievements for the business.
|
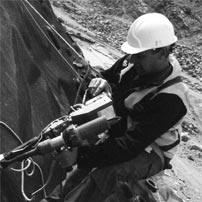 |
Investing in the future
Together with our re-branding exercise we have put in place a substantial investment programme to help us realise our future business aspirations.
We have increased both the size and specification of our specialist equipment thereby augmenting our current plant inventory. We have also invested in the business with new IT systems.
All of these investments will enable us to accept the future challenges of expansion within both our work and Client base, ensuring that Masterlay Limited is the chosen supplier within the lining sector. |
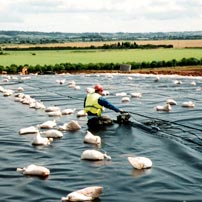 |
Clifton Marsh Installation
Contract:
Clifton Marsh Landfill Site, Frekleton, Preston
Phase 4 cell 2 Basal Liner and Restoration
Area 4 & 5 Capping Construction Works
Client:
SITA (Lancashire) Limited
Principle Contractor:
Ascot Environmental Limited
Details / Unusual or challenging aspects:
Our inaugural installation project required the placement of some 237233sq.m of 1mm thick smooth welded flexible membrane liner to the prepared sub-grade of restoration areas R4 & R5.
A Liner of the more elastic, LLDPE type was selected to accommodate the differential settlement that was anticipated to occur over the restoration areas.
The works were overseen by a client appointed CQA engineer to provide quality assurance of the geomembrane cap in accordance with the construction method statement and CQA Plan. the installation was successfully completed within the required timescale using a combination of fusion (hot wedge) and extrusion welding with outputs of up to 8000sq.m achieved each day.
|
|